About
Find Out More About the Product
The client, Integration Industries 2.0, has asked to design and build an Autonomous Rover. The Rover must be capable of navigating itself with a specified GPS waypoint through rough terrain to drop off a payload and return back to its starting location in a timely manner. In addition, the Rover must demonstrate obstacle avoidance without GPS navigation.
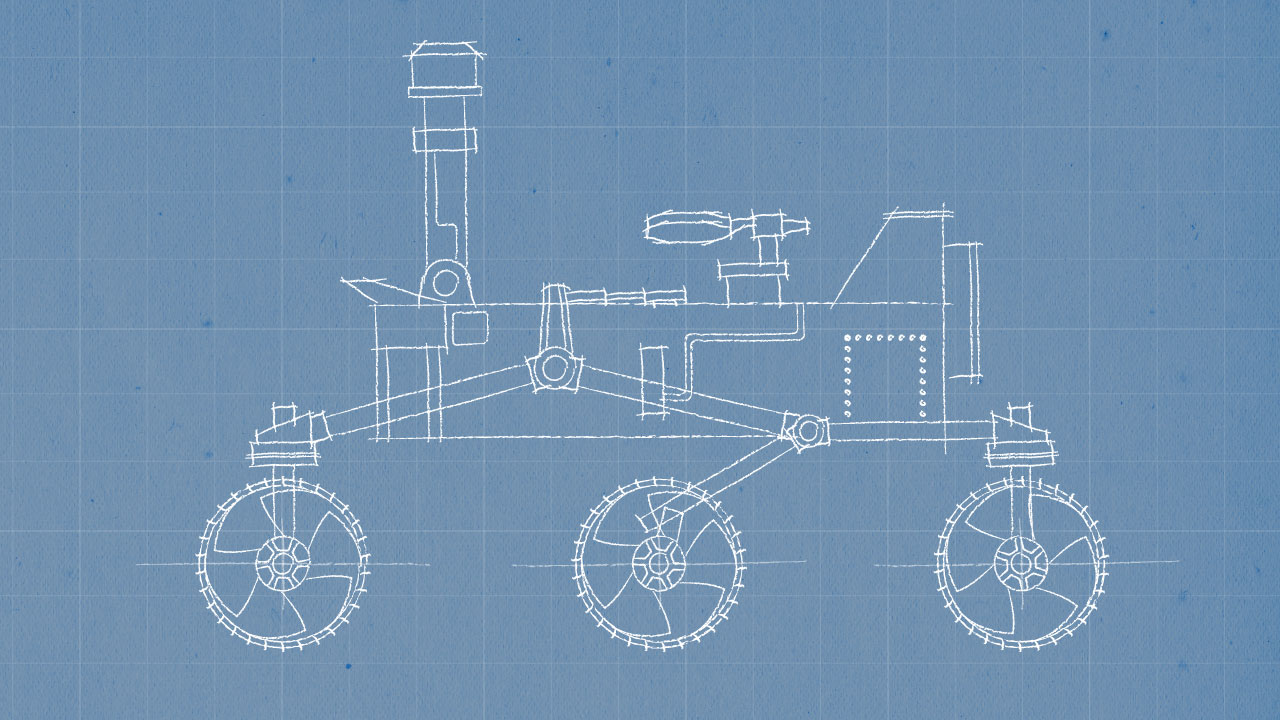
Statement of Work
-
Purpose
The client, Integration Industries 2.0, requested a rover that can drop off a payload to a specified location and return back to its starting position through rough terrain.
-
Scope of Work
The Maverick Rover will need: a chasis, a motor, a program to control how the rover will navigate itself, a sensor to avoid obstacles.
-
Location of Work
The majority of the work will be done in room 105 of Confluence Hall.
-
Period of Performance
The project began on January 23, 2023 and will be finished by May 17, 2023
-
Deliverables Schedule
See project schedule in useful links
-
Acceptance Criteria
The rover will be capable of navigating itself to a specified location to drop off a payload. In addition, the rover will be easily controllable and to set up.
Team
Our Hardworking Team
Our team, Maverick Rovers, are working together to design and create an autonomous rover under certain circumstances which can be found through our site. As upperclassmen in the Mechanical Engineering - Technology program at Colorado Mesa University we are fulfilling these tasks by combining all of our skills and knowledge we have learned thus far. The most prominent skills to complete our design process will include computer programming, computer-aided design (CAD), machining and product development processes.
Product Overview
The autonomous rover will need: a chasis, a program to control how the rover will navigate itself to the waypoint, a sensor that will allow for obstacle avoidance, a retractable trunk to hold and drop off the payload.
Product Specifications
The autonomous rover will weigh under 4 lbs. Contain a chasis that will have enough torque to navigate through rough terrain. Rover must be capable of covering surfaces specified by the customer in about 1 ft/s.
Product Design and Analysis
Have a RF transmittor and reciever to locate the coordinates. Navigate accurately and repeatedly. Navigate rough/uneven terrain and avoid obstacles. Be lightweight and portable.
Customer Requirements
As a team, each member decided how important the customer requirements were on a 0 to 100 point scale. These are the average points distributions.
Overall
Mission 1
1A
- Drive in 10' square pattern, stop at original location and place a marker
- Place the marker within 3' of the rover's original location
- Complete mission in under 60 seconds.
1B
- Read the intended distance from an RF transmitter beacon at the starting location
- Drive straight for 15'-30' and place a marker
- Place the marker within +/- 10% of the specified drive distance
- Complete the mission in under 30 seconds
Mission 2
2A
- Drive in an enclosed 10'x10' area without contacting walls or obstacles for 60 seconds
2B
- Drive forward to a waypoint 30' directly ahead
- Demonstrate avoidance algorithm by continuing to original waypoint after navigating around a single obstacle
- Stop within 5' of the marked waypoint
- Complete mission in under 120 seconds
Mission 3
3A
- Start from an arbitrary location and heading and navigate so that the rover is pointing due North within +/- 20°
- Complete mission in under 180 seconds
Mission 4
4A
- Navigate to specified GPS waypoint
- Stop within 15' of specified GPS waypoint
4B
- Read the GPS coordinates from an RF transmitter beacon placed at the starting location
- Place a marker within 15 feet of the specified waypoint and return to original start location
- Not exceed a cumulative error of 25' for this mission
Engineering Specifications
Using similar decision matrices as the customer requirements, we ranked the importance of the following engineering specifications. These are the average points distributions. The supporting calculations can be found in the engineering analysis.
Concept Generation
Check our Designs
Our techniques included all design ideas by including conditional and promising design ideas. From reverse engineering RC cars and pre-built chassis kits, our team used a matrices method to decide what we thought were most important based on the chassis, movement, and payload drop.
- All
- Chassis
- Movement
- Payload Drop
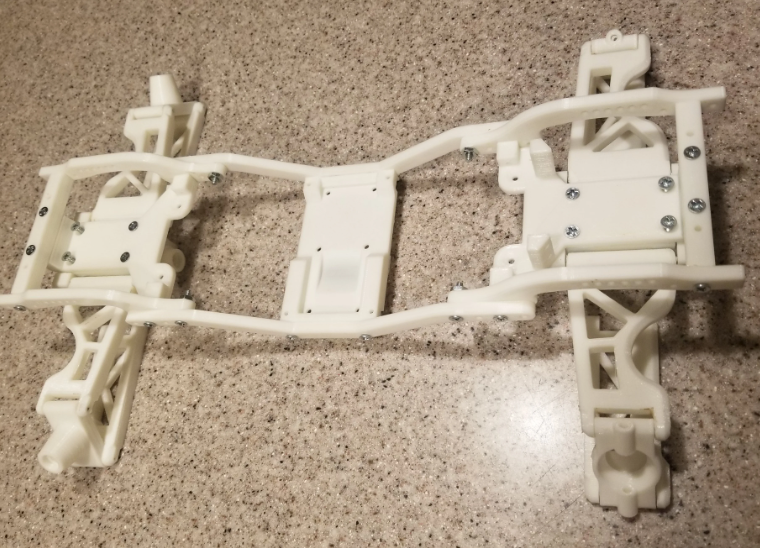
3D Print
Chassis 1
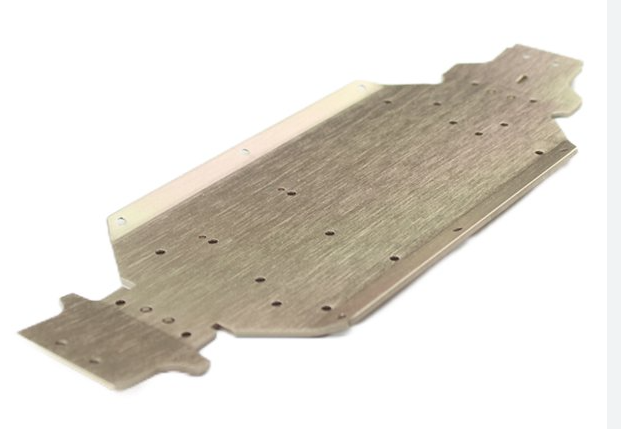
Wood
Chassis 2
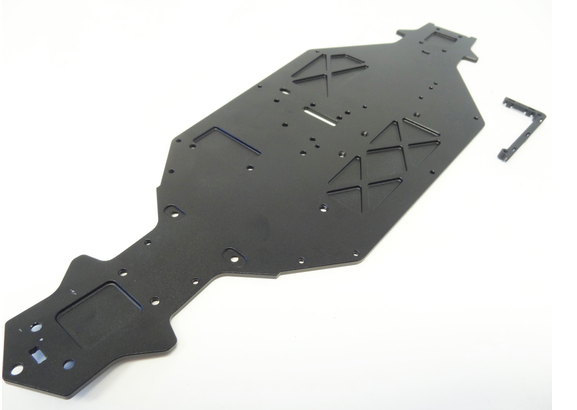
Aluminum
Chassis 3
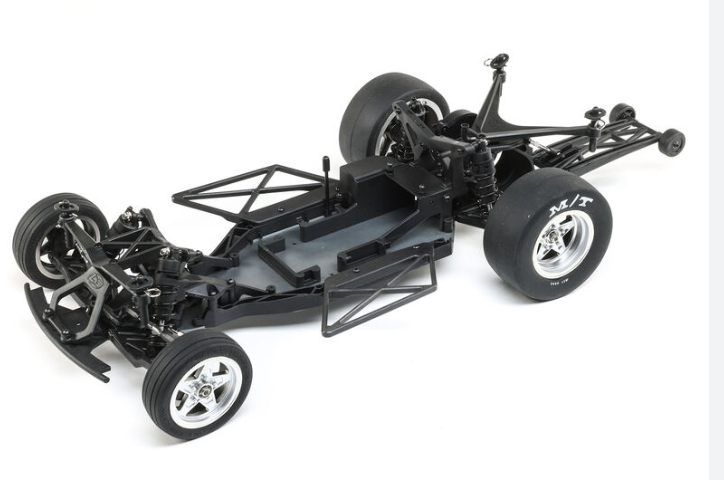
Pre-built 1
Chassis 4
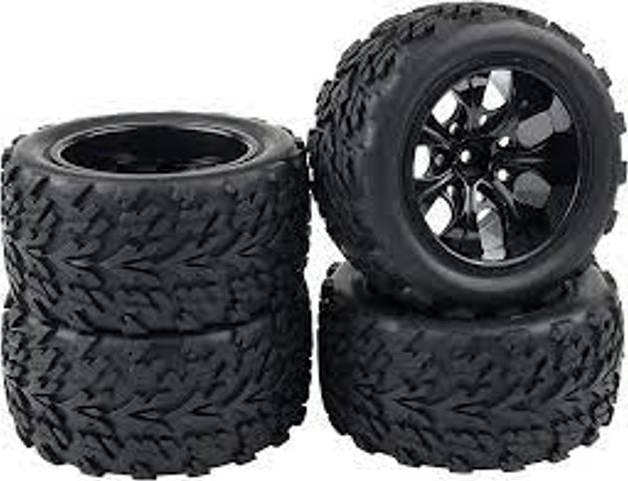
Tires
Movement 1
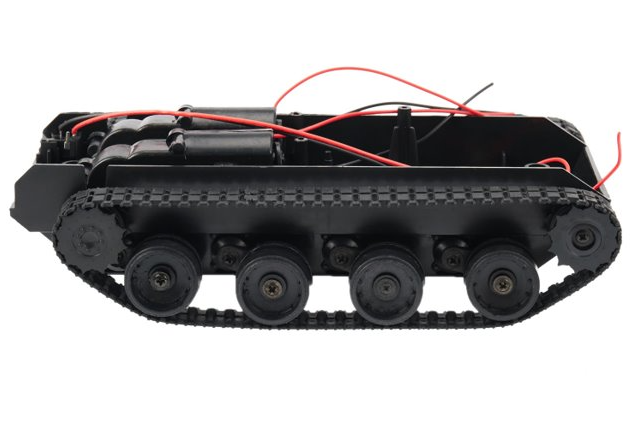
Tank Tread
Movement 2
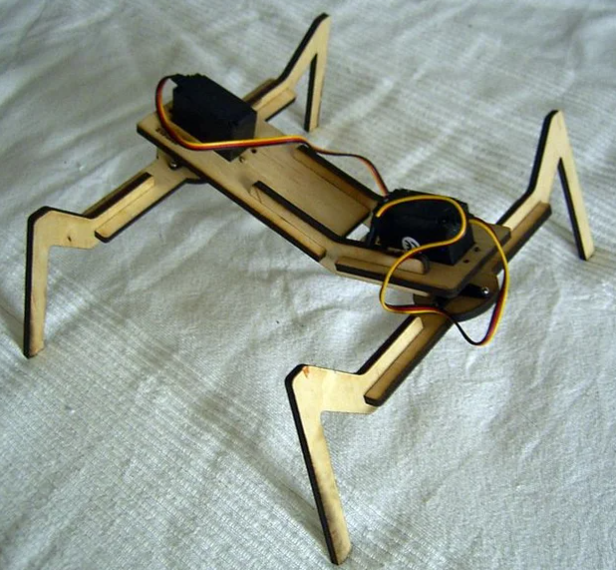
Walker
Movement 3
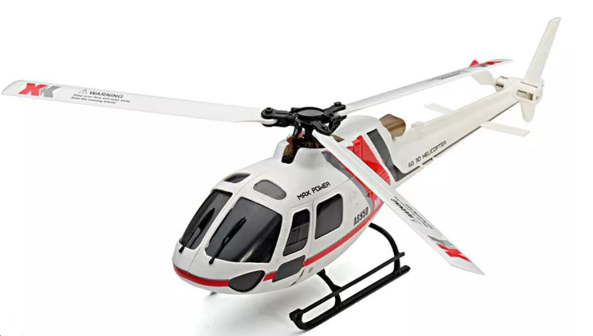
Flying
Movement 4
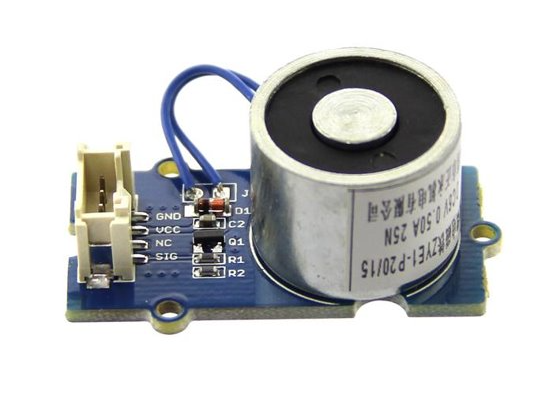
Magnet
Payload Drop 1
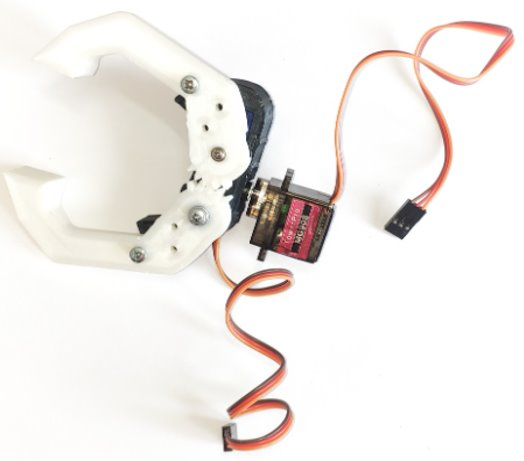
Grip
Payload Drop 2
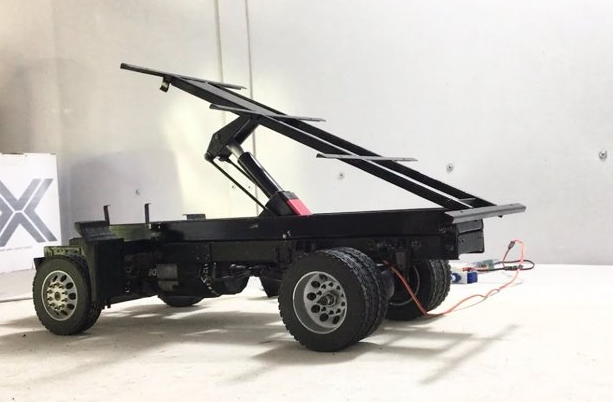
Dump
Payload Drop 3
Concept Evaluation
Promising Concepts
After using a matrices method, the following concepts have been evaluated as most promising
-
Chassis
3D printing and a pre-built kit was noticed to be the most promising since they are capable of holding all modules while being sturdy enough to handle the drop and water test. Mainly focusing on durability and workability/repairs for our engineering analysis. Our team decided to go with the pre-built kit since it would cut on budget costs dramatically because we found an old RC car kit laying around. This won’t affect our quality of our rover since we believe it will function properly with the right hardware and coding.
-
Movement
A tank tread and tires were noticed to be the most promising since they are capable of maneuvering through rough terrain and attaining a tight turning radius. Mainly focusing on turning radius and ability to drive through rough terrain for our engineering analysis. Our team decided to go with the tires for our movement mechanism since they came with the old RC car kit which will cut on costs. We believe the tires will be able turn and ride through rough terrain just as well as the tank tread would.
-
Payload dropping mechanism
A dump and grip system were noticed to be the most promising since they are capable of holding onto the payload till the desired drop zone and are both responsive. Mainly focusing on security while driving and coding complexity for our engineering analysis. Moving forward with the dump system, we believe this system will be the least complicated while still being capable of completing the missions.
Product Generation
Our Product
Design sufficient for all Missions
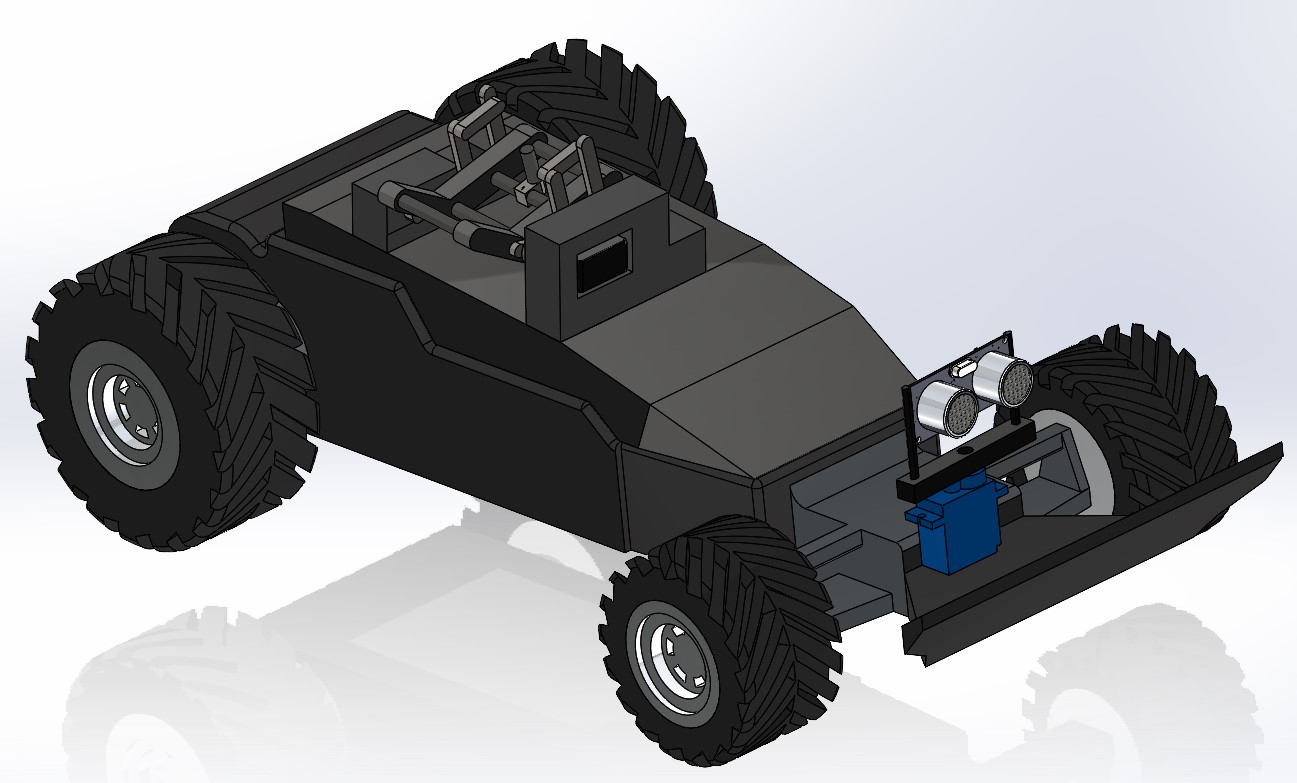
Solidworks Assembly
Autonomous Rover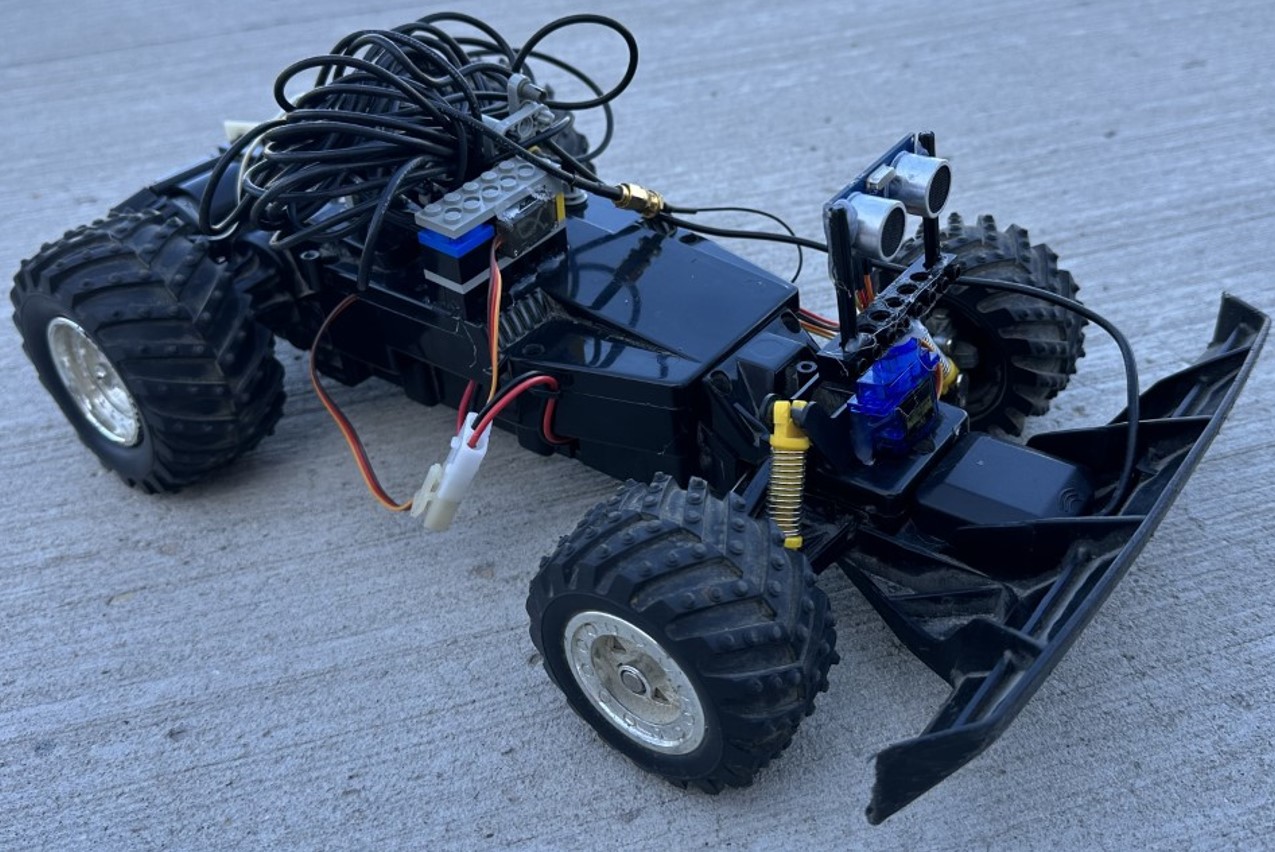